At Barclay Roto-Shred, we engineer our machines to far exceed industry standards. This allows our tire-shredding equipment to stand up to the toughest rigors of the tire-shredding industry like no other brand on the market. One measure of our success is how many Barclay machines are still in operation after 10+ years of extreme use – a testament to our commitment to quality, durability, and efficiency
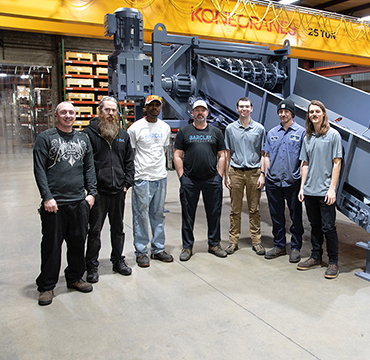
Why Barclay? Because Barclay Tire Shredders have the lowest total cost of ownership to buy, operate, and maintain.
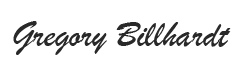
Specifically engineered to make tire shredding effortless.
To become the de facto standard for tire shredding across the globe.
Leverage our years of expertise in engineering and innovation to develop state-of-the-art tire recycling machinery and equipment.
Know Our History
The Prelude
Randy Barclay worked with a leading OEM engineering shredder to help launch the organization’s product line. Following his time there, he designed a tire shredder for SSS Dynamics, employing Mark Diemunsch to create the drawings for the machine. From this, a partnership was born.
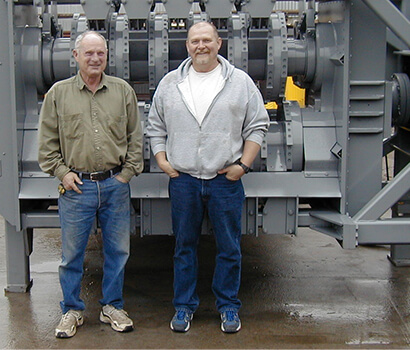
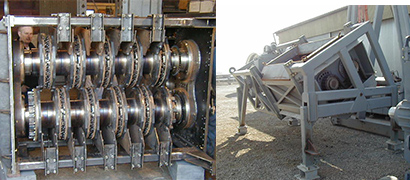
The Beginning
Randy and Mark invented the original 6P Barclay Primary Shredder, a straightforward primary tire shredder that cleanly sheared high volumes of scrap tires into six-inch strips in just seconds. This Barclay tire shredding machine quickly became the workhorse of the tire-shredding industry due to its limited need for maintenance, easy-to-change knives and bases, and its scrap tire-cutting capabilities. Along with the original Barclay Primary Shredder, created a Secondary Shredder. Like today, the goal of the secondary shredder was to reduce pre-processed tires into smaller chips, providing flexible equipment options to tire shredding companies.
A New Era
Randy Barclay retired leaving the business in the capable hands of Mark Diemunsch.
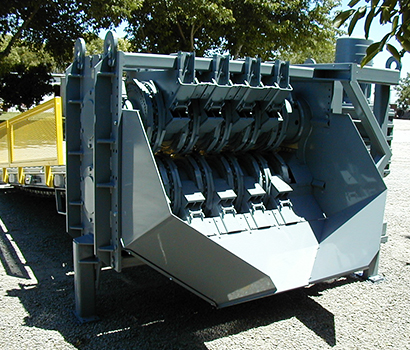
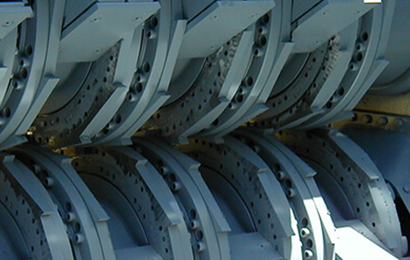
The Start of a Partnership
Barclay Roto-Shred approaches American Cutting Edge to manufacture the knives and bases for their Primary and Secondary Shredders. Confident in their ability to manufacture knives to their exact specifications and precision geometry, Barclay Roto-Shred began having their knives outsourced to American Cutting Edge.
A New Approach
Based on customer feedback, Barclay Roto-Shred reevaluated the end chip size of the 6P Primary Shredder to create a smaller size. To simplify manufacturing and produce a more budget-friendly machine, Barclay designed the new 4.9 Primary Shredder to use the same knives as the 2S Secondary Shredder with 288 knives versus the 240 knives of the original 6P Shredder. With more knives came a better quality cut and smaller end chip sizes.
A New Chapter
2021 saw the retirement of Mark Diemunsch and the sale of Barclay Roto-Shred to its knife manufacturing partner, American Cutting Edge. Dedicated to keeping the Barclay legacy alive, the acquisition came with an expansion in manufacturing facilities in Miamisburg, Ohio to accommodate the full production of all Barclay products.